Radio Frequency Identification (RFID) technology has become a game-changer in warehouse management, offering enhanced inventory visibility, improved accuracy, and increased efficiency. As a project manager overseeing the implementation of an RFID system, understanding the key steps, challenges, and best practices is crucial to ensuring a smooth transition.
Key Steps for Implementing an RFID System
- Define the Objectives
- Identify the primary goals of implementing RFID, such as reducing inventory errors, minimizing theft, or improving tracking accuracy.
- Engage stakeholders early to align expectations and secure buy-in.
- Conduct a Feasibility Study
- Assess the current warehouse infrastructure to determine compatibility with RFID technology.
- Evaluate potential return on investment (ROI) and overall benefits.
- Select the Right RFID Technology
- Passive RFID: Cost-effective and suitable for large-scale inventory tracking.
- Active RFID: Best for real-time tracking of high-value assets.
- Hybrid Systems: Combining both for optimal efficiency.
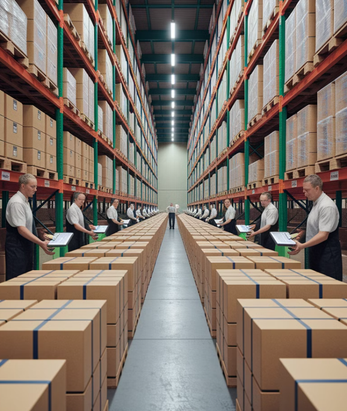
- Choose Software as a Service (SaaS) Applications Implementing RFID requires integration with software solutions for data capture, analytics, and operational insights. Some top SaaS solutions include:
- Impinj – Offers cloud-based RFID solutions for real-time inventory visibility.
- SOTI Connect – A scalable platform for managing RFID devices and warehouse automation.
- Zebra MotionWorks – Provides asset visibility and workforce management capabilities.
- Fishbowl Inventory – A warehouse management system with RFID integration for small to mid-sized businesses.
- Oracle NetSuite WMS – A comprehensive solution for tracking and managing warehouse operations with RFID capabilities.
- Develop a Pilot Program
- Test the RFID system in a small section of the warehouse before a full-scale rollout.
- Monitor key performance indicators (KPIs) to assess effectiveness and address potential issues.
- Integrate with Existing Systems
- Ensure seamless integration with Warehouse Management Systems (WMS), Enterprise Resource Planning (ERP) software, and IoT devices.
- Use APIs and middleware solutions to facilitate data synchronization.
- Train Employees
- Conduct training sessions for warehouse staff, IT teams, and management on RFID technology and new workflows.
- Develop SOPs (Standard Operating Procedures) to guide daily operations and troubleshooting.
- Monitor Performance and Optimize
- Continuously track system performance, identify inefficiencies, and make necessary adjustments.
- Utilize analytics to optimize workflows and improve warehouse operations.
Challenges and How to Overcome Them
- Interference Issues: RFID signals may be affected by metal surfaces or electromagnetic interference. Use proper shielding techniques and test tag placements to mitigate this issue.
- Integration Complexities: Ensure your IT team is involved in integrating RFID data with existing business applications.
- Cost Considerations: RFID implementation can be costly. Prioritize a phased approach and explore leasing options for RFID hardware.
- Change Management: Employee resistance is common. Engage staff early, highlight benefits, and provide comprehensive training.
Final Thoughts
Implementing an RFID system in a warehouse requires careful planning, technology selection, and change management. As a project manager, leveraging SaaS applications, piloting the technology, and continuously optimizing processes will ensure a successful transition. By embracing RFID, warehouses can achieve real-time inventory tracking, reduce operational inefficiencies, and enhance overall productivity.
Are you currently working on an RFID implementation? Share your experiences and challenges in the comments!
#RFID #WarehouseManagement #ProjectManagement #SupplyChain #InventoryTracking #SaaS #Technology #Logistics #Automation #DigitalTransformation #SmartWarehouse #WMS #ERP #TechInnovation #BusinessEfficiency #IoT #ProcessImprovement #WarehouseTech #RFIDTechnology #CloudSolutions
Add comment
Comments